Jaeger-LeCoultre, The Swiss Luxury Watchmaker, Exhibits The Remarkable Atmos Regulateur 'Cherry Blossom' at Venice's Homo Faber
- 15th Apr 2022
- 1805
- 0

Jaeger-LeCoultre, a Swiss luxury watch and clock maker, unveiled the extraordinary Atmos Régulateur 'Cherry Blossom' at Homo Faber in Venice.
The Atmos Régulateur 'Cherry Blossom' is a one-of-a-kind piece of art, showing the clock's movement inside a clear glass cabinet set between two striking black Grand Feu enamel panels. A cherry blossom branch, hand-painted in enamel, runs effortlessly from one side to the other panel, over the dial ring. Petals strewn across the area, as though shook loose by a passing wind.
SAKURA CELEBRATES THE CREATIVITY OF HUMAN BEINGS
This is the biggest enamelled item ever done at La Grande Maison, requiring 200 hours of focused effort by skilled craftsmen in Jaeger-Métiers LeCoultre's Rares® workshop. While the enamellers have perfected the processes for enamelling watch casings and dials, the huge size of this project posed unique obstacles. To accomplish it, the atelier's artists collaborated closely, spending many hours doing preparatory research, sharing ideas, testing, and conducting trials before enamelling could begin in earnest. Materials and procedures were re-examined and revised – as was the need for a new kiln capable of handling such enormous pieces.
"A one-of-a-kind work of art, the Atmos Régulateur 'Cherry Blossom' is the biggest Grand Feu enamel piece ever manufactured by Jaeger-LeCoultre, taking 200 hours for enamelling alone."- Lionel Favre, Design Director
THE COLUMNS
Copper was discovered to be more suited for the panels – which measure 196mm by 105.2mm – than gold, which is often used for enamelling on watches. To acquire the needed depth and consistency of black on such enormous surfaces, the enamellers had to master the 'dry enamelling' method of sifting powdered pigment onto copper plates (much like dusting the top of a cake with icing sugar), repeating the procedure many times. Following each layer, the panels were fired, cooled, and properly flattened - each step posing the danger of bubbling, cracking, or dust particles, all of which would damage the work.
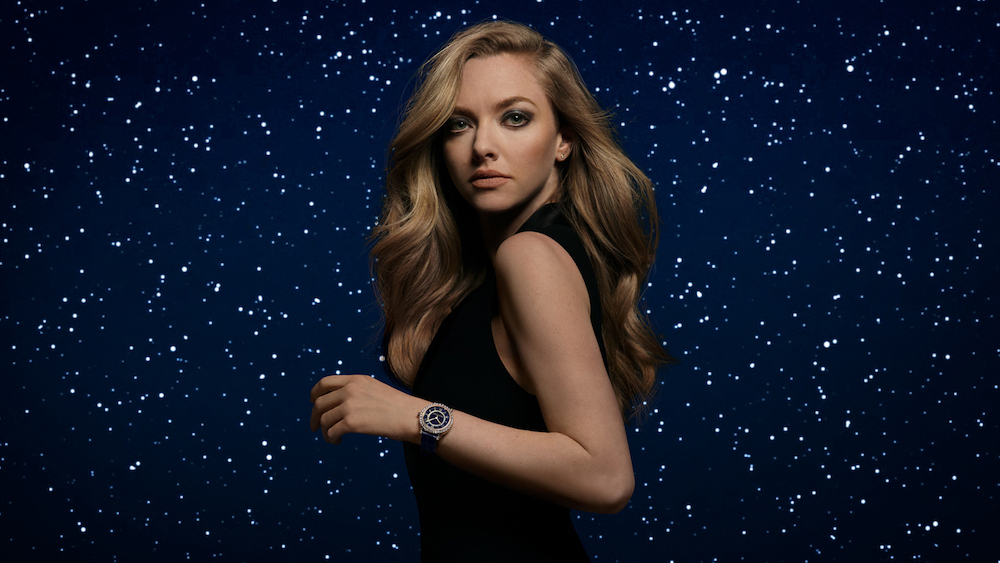
THE DIALS
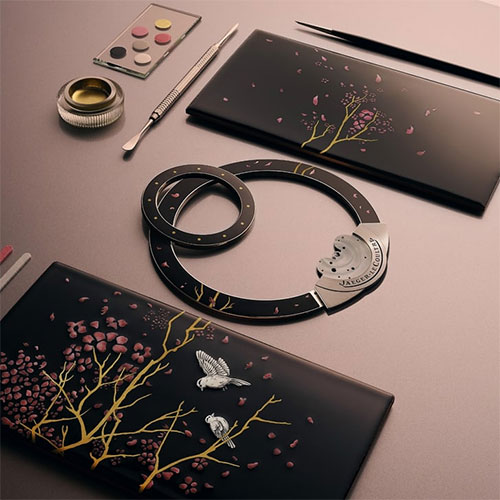
Silver was chosen as the ideal material for the two dial rings – despite the fact that it is a soft metal and hence less resistant to firing at the high temperatures necessary for grand feu enamel. Normally, the rear of an item is prepped with 'contre-email' to avoid distortion, but this was impossible in this instance due to the dial being visible from behind. The rings were hollowed out to create a trough for applying the enamel. Then, with regard to the panels, there was the issue of numerous firings.

ENAMELLING IN MINIATURE
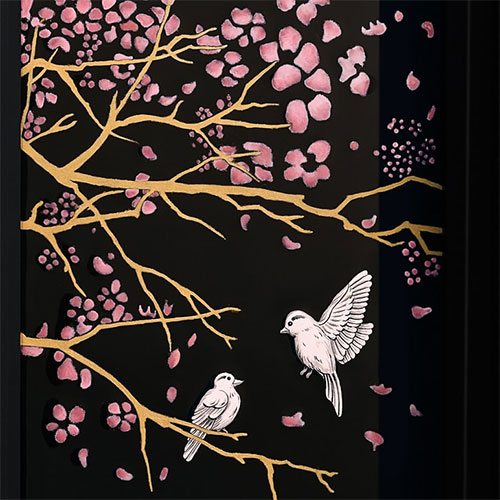
Finally, after the black enamel backgrounds were perfected, the miniature painter's work could begin, bringing with it the nearly conflicting need for artistic flare and exact accuracy. As with the black enamel, this piece was created in a sequence of layers, each of which required firing, with each subsequent firing posing the danger of ruining all that came before. To succeed in this line of work requires an exceptional amount of subtlety and a level of skill that can only be acquired through numerous years of experience.
A TIMEKEEPING REVOLUTION
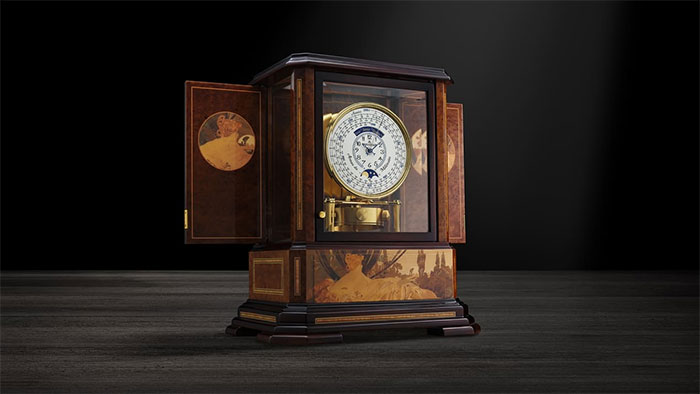
The Atmos clock survives on air thanks to an innovative mechanism devised by Jean-Léon Reutter in 1928 and commercialised by Jaeger-LeCoultre in the 1930s. Since its inception, its magnificent design has been reinterpreted and recrafted, bringing it to the status of icon. The Atmos, dubbed the "President's Clock," was the Swiss Confederation's official gift.
Source: jaeger-lecoultre.com
Comments
No comments yet.
Add Your Comment
Thank you, for commenting !!
Your comment is under moderation...
Keep reading luxury post